Der Schlüssel zu effizienten Hochleistungsbatterien
Niedrige Widerstände exakt vermessen
Am Anfang der Zufall: Mitte der 80er-Jahre entwickelte der japanische Messtechnik-Hersteller HIOKI ein AC-Milliohm-Meter, mit dem sich Kontaktwiderstände von Schaltern und Relais besser vermessen lassen sollten als mit den bisher gebräuchlichen DC-Milliohm-Metern. Dabei entkoppelte HIOKI in dem neuen Gerät auch den Prüfling galvanisch vom Messkreis, womit die Messungen unabhängig von unterschiedlichen Potentialen zwischen den beiden Messpunkten wurden.
Etwa zeitgleich brachte der japanische Forscher Akira Yoshino den von John B. Goodenough entwickelten Lithium-Cobaltdioxid-Akkumulator zur Marktreife. Bei der Vermessung des Widerstandes dieser neuen Akkumulatoren stellte sich das AC-Messverfahren als besonders geeignet heraus, wobei aufgrund der unterschiedlichen Potentiale zwischen den beiden Polen eine galvanische Trennung zwischen Prüfling und Messkreis erforderlich war.
So wurde der ursprünglich für das Vermessen von Kontaktwiderständen entwickelte „AC mΩ Hi Tester 3225“ für HIOKI zum Beginn einer inzwischen 35 Jahre dauernden Erfolgsgeschichte rund um das Thema Lithium-Ionen-Batterie. Aus dem ursprünglichen Milliohm-Meter entwickelte sich dabei eine ganze Produktfamilie an Batterietestern für das Vermessen von Zellen, Modulen und Packs.
Die Wichtigkeit kleiner Widerstände
Im Produktionsprozess von Lithium-Ionen-Zellen oder -Batterien kommt der Batterietester erst zu einem recht späten Zeitpunkt zum Einsatz. Widerstandswerte werden jedoch schon viel früher im Prozess überprüft, denn das Sicherstellen möglichst geringer und idealerweise immer gleicher Widerstandswerte ist mitentscheidend für die Qualität der Batterie. Das hat vor allem zwei Gründe.
Zum einen ist ein kleiner Gesamtwiderstand eines Batteriesystems entscheidend dafür, dass man beispielsweise beim Beschleunigen eines E-Sportwagens in den Sitz gedrückt wird. Denn dafür muss die Batterie in der Lage sein, den Motor mit hohen Strömen zu versorgen. Den Zusammenhang zum Widerstand erklärt ganz einfach das Ohmsche Gesetz.
Stellt man U=RI um zu I=U/R , dann sieht man, dass ein kleiner Widerstand R bei gleicher Spannung U einen großen Stromfluss I bedeutet.
Zum anderen sorgt jeder Widerstand in einem Batteriesystem dafür, dass elektrische Energie als Wärmeenergie verloren geht. Das ist kein spezifisches Phänomen bei Batterien, sondern geht auf das allgemeingültige Stromwärmegesetz zurück – auch bekannt unter dem Namen „Erstes Joulesches Gesetz“.
Die elektrische Verlustleistung, die am Widerstand abfällt, kann ganz klassisch mit P=UI beschrieben werden. Ersetzt man die Spannung U durch RI aus dem oben erwähnten Ohmschen Gesetz, dann erhält man P = UI = (RI)I = RI² . Man sieht also wie sich die Verlustleistung P mit steigendem Widerstand R vergrößert.
AC oder DC?
Beim Vermessen von Widerständen gerade im Zusammenhang mit Batterien unterscheidet man zwischen zwei Messverfahren – der AC- und der DC-Widerstandsmessung. Mit der DC-Widerstandsmessung ist an dieser Stelle nicht die DC-Innenwiderstandsbestimmung einer Batterie gemeint, bei der durch das Entladen der Batterie mit einer Last über die Spannungsänderung der Innenwiderstand bestimmt wird. Vielmehr ist hier die Widerstandsmessung mit einem 4-Draht-Messverfahren gemeint.
Zum Einsatz kommt das DC-Messverfahren beispielsweise bei der Vermessung von Kontaktwiderständen. Geräte, die mit diesem Verfahren arbeiten sind Multimeter, (DC-) Widerstandsmessgeräte oder Isolationstester. Das AC-Messverfahren findet sich dagegen in Batterietestern oder LCR-Messgeräten.
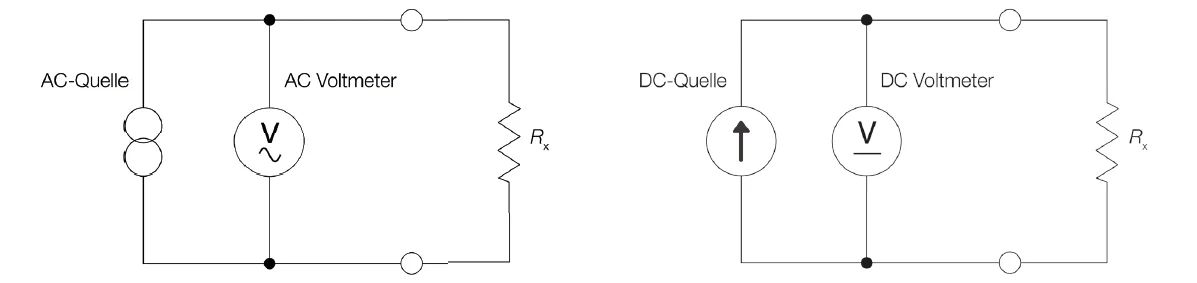
Bild 1: AC und DC Widerstandsmessung im Vergleich.
Elektrodentests
Durchläuft man den Fertigungsprozess einer Lithium-Ionen-Batterie chronologisch, findet eine wichtige elektrische DC-Widerstandsmessung bereits recht früh nach dem Beschichten der Elektroden mit der Aktivmasse statt. Dabei wird lithiumlegiertes Material unter Druck und bei entsprechenden Temperaturen auf das Elektrodenmaterial aufgetragen.
Eine anschließende Widerstandsmessung erlaubt das Bestimmen des spezifischen elektrischen Widerstands der aufgetragenen Aktivmasse sowie das Feststellen des Übergangswiderstands zwischen dem Aktivmaterial und der Elektrode. Allerdings ließen sich diese beiden Werte bis vor wenigen Jahren nicht einfach separat bestimmen – besonders die Vermessung des Übergangswiderstands zwischen Aktivmasse und Elektrodenmaterial stellte hier eine Herausforderung dar. Das änderte sich mit der Markteinführung eines neuen Elektrodenwiderstandsmesssystems – dem RM2610 von HIOKI.
HIOKIs RM2610 ist im Prinzip ein DC-Widerstandsmessgerät. Statt mit einer klassischen 4-Draht-Messung arbeitet der RM2610 jedoch mit einem Tastkopf, bei dem auf einer Gesamtfläche von 1 mm2 insgesamt 42 federnde Kontakte angeordnet sind. Während der Messung werden zwischen den Kontakten eine Reihe an DC-Widerstandsmessungen vorgenommen. Anhand dieser Messergebnisse werden dann mit Hilfe eines mathematischen Modells und bekannten Parametern der spezifische Widerstand der Aktivmasse sowie der Übergangswiderstand zwischen Aktivmasse und Elektrode berechnet.
Die bekannten Parameter sind dabei einfach bestimmbare Größen wie die Stärke des Elektrodenmaterials, die Schichtdicke der Aktivmasse und der Wert der elektrischen Leitfähigkeit des Elektrodenmaterials. Das Elektrodenmaterial der Anode ist üblicherweise Kupfer, während für die Kathode in der Regel Aluminium gewählt wird. Kupfer kann als Kathodenmaterial nicht verwendet werden, da es an der Kathode korrodieren würde. Umgekehrt ist Aluminium als Anodenmaterial ungeeignet, da es mit Lithium reagiert.
Auch wenn der RM2610 inzwischen vielfach als Prüfgerät in der Produktion von Lithium-Ionen-Zellen zum Einsatz kommt, wurde er eigentlich für den Einsatz in Entwicklungsabteilungen konzipiert. Ziel war es, den Entwicklungsprozess von Zellen mit neuen Materialien zu verkürzen, indem eine Möglichkeit geschaffen wurde, bereits nach Fertigstellung der beschichteten Elektroden eine Aussage über die zu erwartende Güte der fertigen Zelle treffen zu können. Diese Möglichkeit war so einmalig und prozessverbessernd, dass HIOKIs Elektrodenwiderstandsmessystem noch in der Prototypenphase bei mehreren Dutzend Kunden in Asien zum Einsatz kam.
Bild 2: Vermessung von Übergangswiderständen bei Elektroden – RM2610 .
Widerstände von Schweißkontakten
Ganz klassisch mit einer 4-Draht-Messung laufen dagegen DC-Widerstandsmessungen beim Bestimmen von Kontaktwiderständen nach dem Herstellen von geschweißten Verbindungen ab. Egal, ob es sich bei diesen geschweißten Verbindungen um das Anbringen von Leistungsanschlüssen bei einer Pouch-Zelle oder um das Verbinden einer Zelle mit einer Stromschiene handelt – im Anschluss sollte in jedem Fall der Kontaktwiderstand geprüft werden, um gerade an dieser Stelle das Entstehen einer widerstandsabhängigen Wärmequelle zu vermeiden.
4-Draht-DC-Widerstandsmessungen kann man mit fast jedem Digitalmultimeter für den Labor- oder Industriebereich vornehmen. Für das Vermessen von Kontaktwiderständen in der Produktion gibt es allerdings einige wichtige Gründe die Messung mit einem speziell dafür ausgelegten Widerstandsmessgerät vorzunehmen.
Der erste wichtige Grund ist der Messbereich für den Widerstand. Bei einem verbreiteten und ohne Frage erstklassigen 7-½-stelligen Digitalmultimeter eines der bekannten Hersteller ist der kleinste Widerstandsmessbereich 1 Ω. Das klingt auf den ersten Blick beeindruckend, allerdings sollten die Kontaktwiderstände von Schweißkontakten bei Lithium-Ionen-Batterien idealerweise unterhalb von 0,1 mΩ liegen. HIOKIs Widerstandsmessgerät RM3545 erfüllt diese Anforderung mit seinem kleinsten Messbereich von gerade einmal 10 mΩ bei einer Auflösung von 0.01 µΩ problemlos.
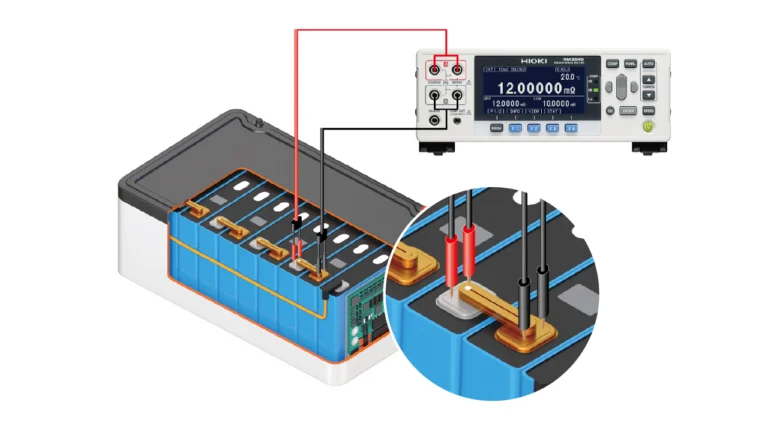
Bild 3: Vermessung von Schweißkontaktwiderständen – RM3545.
Hohe Prüfgeschwindigkeit für die Produktion
Neben einem sehr kleinen Messbereich verfügt HIOKIs RM3545 auch über eine weitere, im Produktionsumfeld sehr sinnvolle Funktion – die Prüfung des Kontakts zwischen Messgerät und Prüfling bei der Messung: Hierbei wird das Prinzip der 4-Draht-Messung genutzt, um sicherzustellen, dass alle 4 Messkontakte sauber für die Messung am Prüfling anliegen. Durch diese Funktion lässt sich verhindern, dass Messungen aufgrund falsch anliegender Messkontakte als „schlecht“ gewertet werden, und dadurch einwandfreie Produkte fälschlicherweise aussortiert werden.
Ein weiterer, ganz wesentlicher Grund, der für den Einsatz eines speziellen Widerstandsmessgeräts spricht, ist die Messgeschwindigkeit: Vom Start der Messung bis zur Ausgabe des Messergebnisses vergehen beim RM3545 in der schnellsten Einstellung lediglich 2,2 ms. Aufgrund der großen Anzahl von zu vermessenden Schweißkontakten in einer Batterieproduktionslinie können auf diese Weise viele Kontaktprüfungen mit wenigen Messgeräten durchgeführt werden.
Bild 4: HIOKIs RM3545.
An dieser Stelle werden Leser mit Produktionserfahrung völlig zurecht einwenden, dass der mechanische Transport eines Prüflings deutlich länger dauert als wenige Millisekunden, was den Vorteil einer sehr hohen Messgeschwindigkeit im Gesamtkontext deutlich relativiert. Um daher aus der hohen Messgeschwindigkeit effektiven Nutzen für die Fertigung zu ziehen, gibt es von HIOKI mit dem RM3545-02 eine Gerätevariante mit Einschüben für Multiplexerkarten.
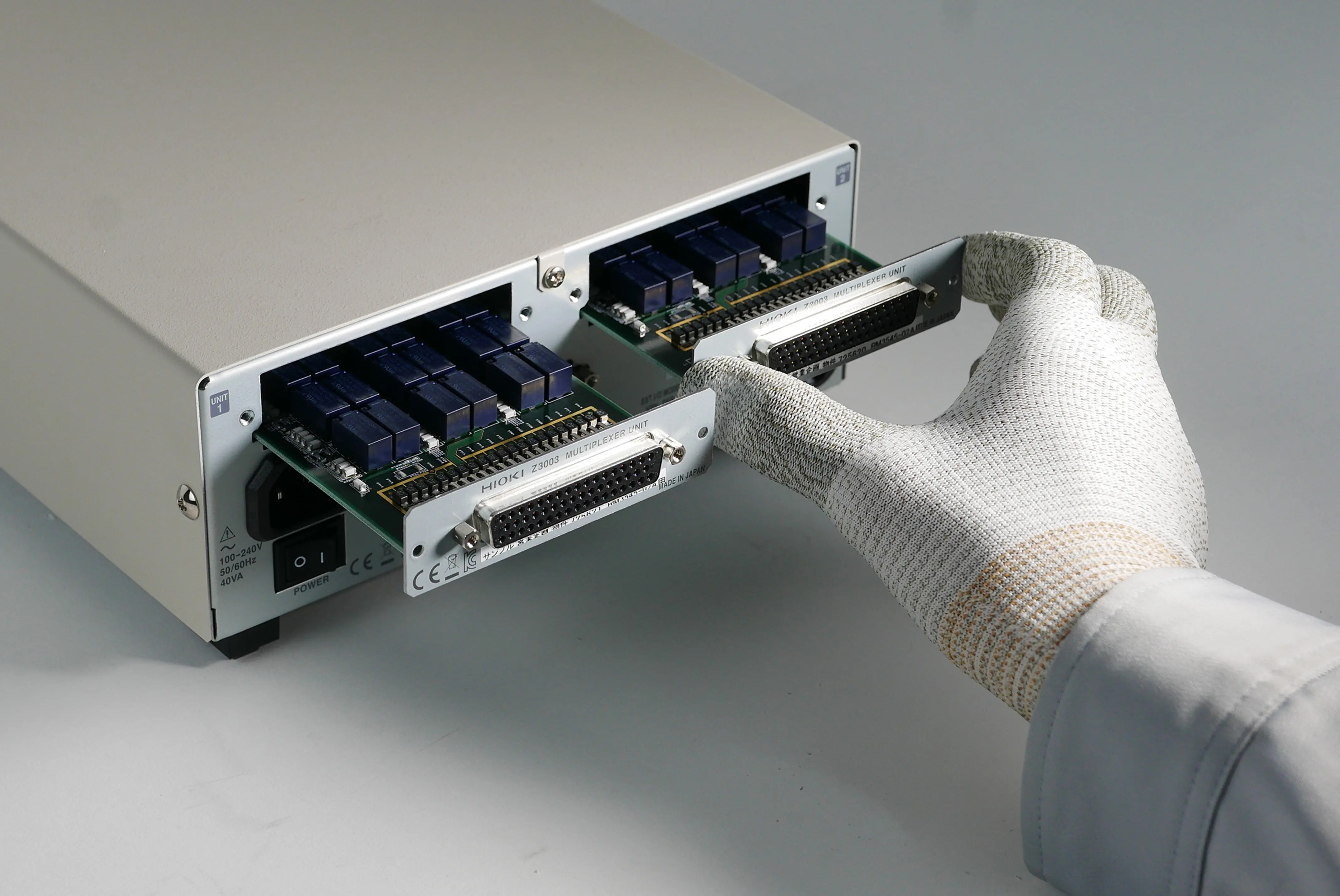
Bild 5: Multiplexeinschübe zur Verwendung in der Fertigung.
Durch das Hinzufügen von zwei der optional erhältlichen Multiplexerkarten erhält ein einzelnes Widerstandsmessgerät die Fähigkeit, in kürzester Zeit bis zu 20 verschiedene 4-Draht-Messungen nacheinander durchzuführen, wenn die Prüflinge mechanisch „im Block“ der Messvorrichtung zugeführt werden. Sollte diese Anzahl an Messkanälen nicht ausreichend sein, weil beispielsweise sämtliche Schweißkontakte eines ganzen Batteriemoduls in einem Schritt vermessen werden sollen, dann gibt es immer noch keine Notwendigkeit, mehrere RM3545 nebeneinander zu betreiben, deren parallele Ansteuerung die Integration deutlich erschweren würde.
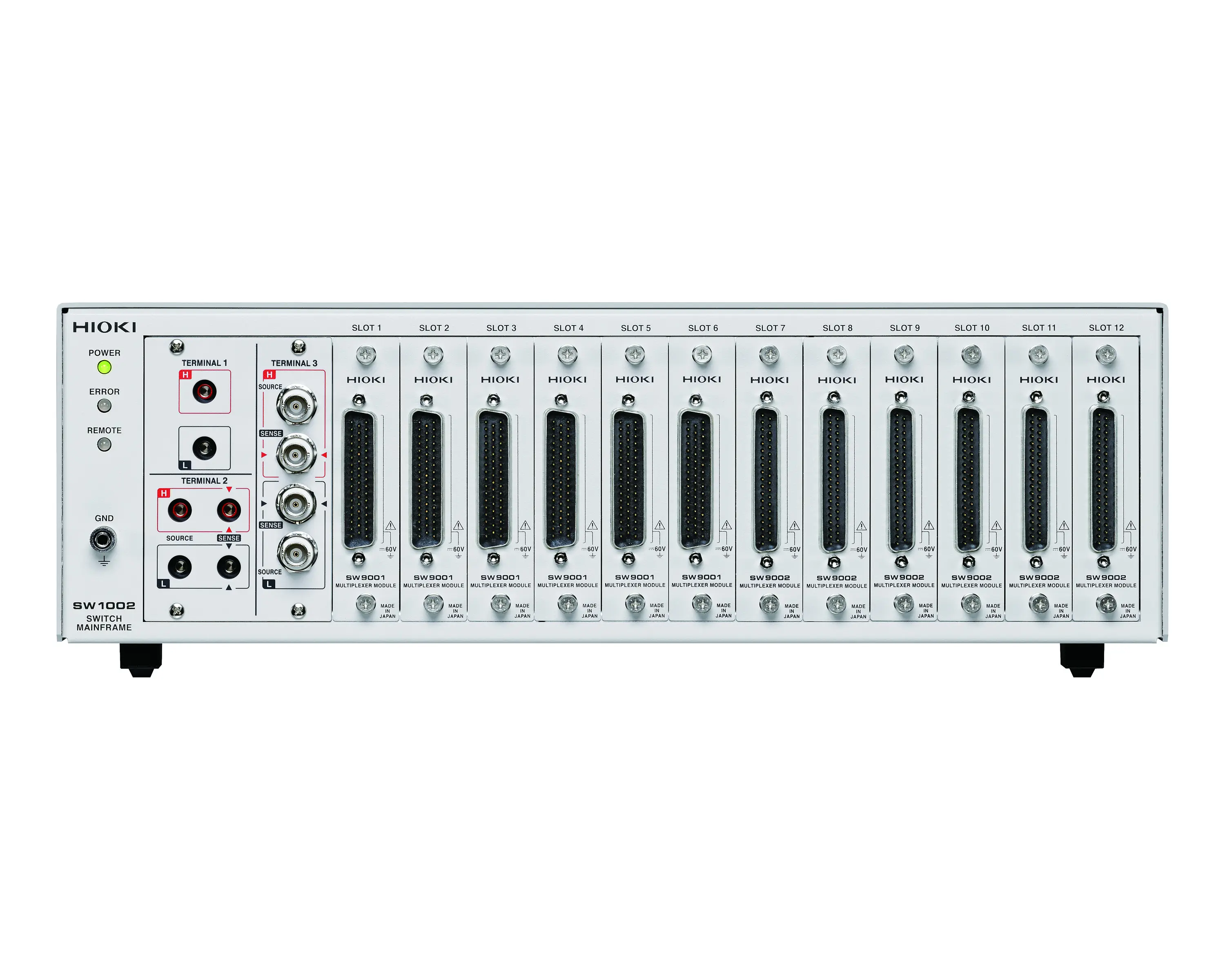
Bild 6: 132 Messkanäle mit einem Messgerät.
In diesem Fall empfiehlt sich die Verwendung eines separaten Multiplexer-Systems. HIOKI bietet ein solches System in verschiedenen Ausführungen an, und ermöglicht in einer für 4-Draht-Messungen ausgelegten Konfiguration das Ansteuern von bis zu 132 Kanälen mit einem einzigen Messgerät wie dem RM3545 (Konfiguration: SW1002 + 12x SW9001). Die Multiplexereinheit ist dabei nicht auf die Verwendung mit Widerstandsmessgeräten beschränkt, sondern kann ebenso mit HIOKIs Batterietestern, Impedanzmetern oder Voltmetern verwendet werden – vorausgesetzt die Messspannungen liegen unterhalb von 60 V.
Wenn man sich einen Messaufbau mit den gerade beschriebenen 132 Kanälen vorstellt, die beispielsweise dazu verwendet werden, bei einem Batteriemodul die Schweißkontakte für die Verbindungen zu Stromschienen zu vermessen, dann sprechen wir aufgrund der 4-Draht-Messmethode nicht nur von über 500 benötigten Messleitungen, sondern auch von über 250 mechanischen Prüfkontakten. Technisch ist dies möglich. Allerdings bietet sich insbesondere bei zylindrischen Zellen in einem Modul eine andere Lösung an.
Die Alternative an dieser Stelle ist ein Flying-Probe-Tester mit dem etwas kryptischen Namen FA1240-W800. Diese Geräte werden üblicherweise für das Testen von bestücken Leiterplatten verwendet, und sind in der Lage, in bis zu 25 ms pro Test unter anderem 4-Draht-Widerstandsmessungen durchzuführen. Am Ende spielt es aber keine Rolle, ob es sich beim Prüfling um eine bestückte Leiterplatte handelt, oder aber um ein Batteriemodul, bei dem Schweißkontakte vermessen werden.
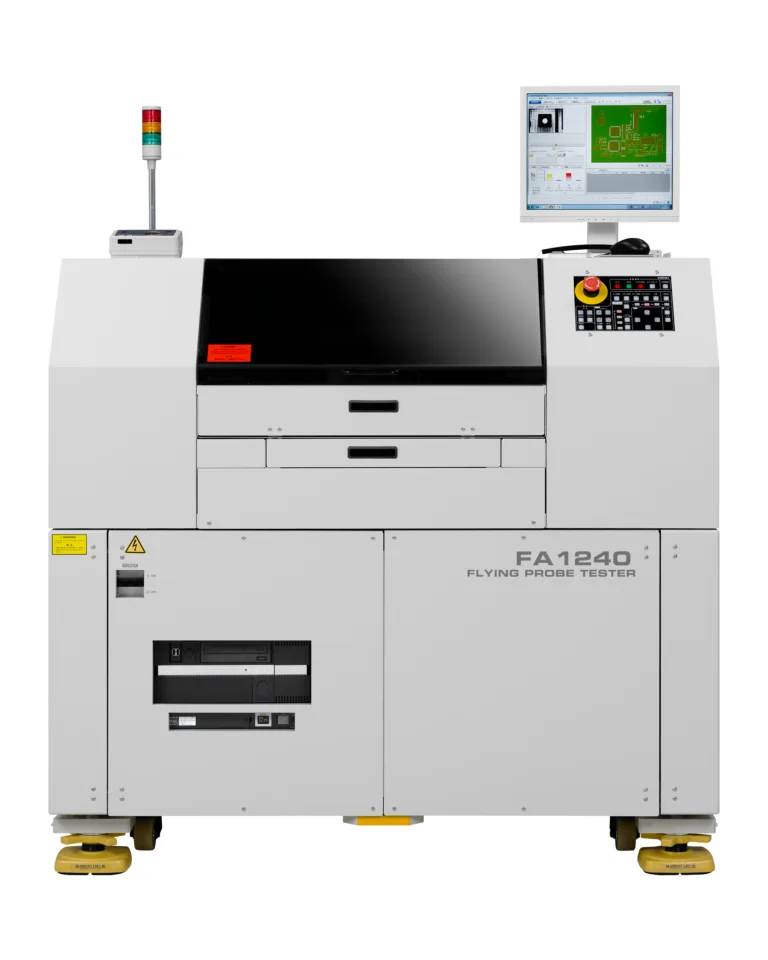
Bild 7: Schweißkontakte vermessen mit Flying-Probe-Tester.
Der Einsatz eines Flying-Probe-Testers hat am Beispiel „Schweißkontakte bei Batteriemodulen vermessen“ einen weiteren Vorteil gegenüber der Anordnung mit festen Prüfkontakten – sei es in der zuvor beschriebenen Variante oder alternativ mit einem „Bed of Nails“; denn während bei bestückten Leiterplatten die Prüfpositionen wirklich immer die gleichen sind, so weichen diese bei einem Batteriemodul mit hunderten von Zellen in der Realität aufgrund von Produktionstoleranzen immer ein wenig voneinander ab. Der Schweißkontakt muss aber präzise vermessen werden.
Der Flying-Probe-Tester FA1240 erlaubt es, für jedes Batteriemodul vorher eine Positionsdatei einzulesen. Diese kann mit der richtigen Kamera und geeigneter Analysesoftware individuell für jedes Batteriemodul erstellt werden. Messfehler aufgrund von mechanischen Produktionstoleranzen sind auf diese Weise ausgeschlossen.
Batterietester für Schweißkontakte?
Eine Frage, die regelmäßig an HIOKI gerichtet wird, ist, ob man einen vorhandenen Batterietester auch für die Vermessung von Kontaktwiderständen verwenden kann. Es gibt einen technischen Grund, der dafürspricht, aber gewichtigere Gründe, die dagegensprechen.
Für den Einsatz des beim Batterietester verwendeten AC-Messverfahrens zum Vermessen von Kontaktwiderständen spräche, dass die elektromotorische Kraft – auch Urspannung genannt – bei diesem Messverfahren keine Rolle spielt. Denn vereinfacht gesagt handelt es sich bei der elektromotorischen Kraft um einen DC-Offset, der bei der Kontaktierung von unterschiedlichen Metallen entsteht. Ein DC-Offset kann bei einer AC-Messung aber ignoriert werden.
Bild 8: Der Defacto-Standard in der Batterieproduktion – BT3562A.
Bei dieser Urspannung handelt es sich um eine sehr kleine Spannung, die bei Widerstandsmessungen im Ohmbereich keinen messbaren Einfluss hat. Kontaktwiderstände bewegen sich aber durchaus im Mikroohm-Bereich, und hier gewinnt auch ein sehr kleiner DC-Offset an Relevanz für das Messergebnis. Wichtig an dieser Stelle ist daher anzumerken, dass das bereits erwähnte DC-Widerstandsmessgerät RM3545 über eine „Offset Voltage Compensation“-Funktion verfügt, mit deren Hilfe der Einfluss der Urspannung minimiert wird.
Gegen den Einsatz von Batterietestern für die Vermessung von Kontaktwiderständen sprechen Wirbelströme, die bei einer 4-Draht-Messung in den Messleitungen auch bei Messfrequenzen von 1 kHz entstehen können. Wie bei der Urspannung haben diese Wirbelströme bei größeren Widerständen keine Bedeutung – bei den sehr niedrigen Kontaktwiderständen haben sie aber einen Einfluss auf das Messergebnis. Schwierig ist dabei, dass Wirbelströme beim gleichen Prüfling abhängig von der Führung der Messleitung bereits unterschiedliche Größen aufweisen können. Wird die Messleitung beispielsweise an einem (magnetischen) Stahlblech wie einem Gehäuse vorbeigeführt, so kann dies ein anderes Messergebnis ergeben, als wenn die Messleitungen beim gleichen Prüfling etwas anders geführt werden. Das ist ein Grund, warum es beim Vermessen von Kontaktwiderständen mit einem Batterietester schwierig sein kann, wiederholbare bzw. exakt vergleichbare Messergebnisse zu erhalten.
Ein weiterer Grund ergibt sich beim Vergleich der Genauigkeiten der beiden Messmethoden: Einer der weit verbreitetsten Batterietester im Produktionsumfeld ist HIOKIs BT3562A. Bei diesem Batterietester liegt die Grundgenauigkeit bei der Widerstandsmessung bei 0,5 %. Das ist für ein AC-Widerstandsmessgerät ein sehr guter Wert. Ein DC-Widerstandsmessgerät wie der RM3545 weist dagegen aber eine Grundgenauigkeit von 0,006 % auf.
Pair Matching von Zellen
Zu Beginn dieses Texts wurde beschrieben, dass mitentscheidend für die Qualität einer Batterie nicht nur kleine, sondern auch gleiche Widerstandswerte sind. Die gleichen Widerstandswerte sind dabei ganz besonders bei Zellen relevant, die in Modulen und Packs zusammengeschaltet werden.
Bei einer Reihenschaltung von Batteriezellen würde eine einzige Zelle mit einem größeren Widerstand wie ein Flaschenhals auf das Gesamtsystem wirken. Der größere Widerstand würde nicht nur für eine erhöhte Temperatur in der Anordnung sorgen, die einen negativen Einfluss auf die Lebensdauer hätte. Auch wäre diese Zelle schneller entladen als die anderen. Im normalen Leben sorgt ein Batteriemanagement-System dafür, dass diese Zellunterschiede ausgeglichen werden, und für den normalen Anwender nicht erkennbar sind.
Ein anderes Bild ergibt sich, wenn die Batterie nicht nur für ein normales E-Auto, sondern beispielsweise für einen Rennwagen der berühmten Königsklasse verwendet wird. Oder wenn eine entsprechend ausgelegte Batterie die gesamte Stromversorgung für ein Expeditionsfahrzeug übernimmt. In beiden Fällen ist es von Vorteil, Serienstreuungen so gut wie möglich auszuschließen.
Bild 9: Elektrochemische Impedanzspektroskopie (EIS) mit dem BT4560.
Erreicht werden kann dies durch ein „Pair Matching“ der einzelnen Zellen. Dabei wird durch elektrochemische Impedanzspektroskopie bei verschiedenen Frequenzen die Impedanz der einzelnen Zellen ermittelt. Bildlich gesprochen ergeben die Impedanzwerte, bestehend aus ohmschem Widerstand und Blindwiderstand, zusammengefasst für jede Zelle eine Ortskurve (Nyquist-Plot). Legt man diese Ortskurven übereinander, so kann man jene Zellen zu einem Modul oder Pack zusammenfassen, deren Ortskurven am nächsten beieinander liegen.
HIOKIs BT4560 Battery Impedance Meter ist für diese Messungen auch deshalb ein geeignetes Gerät, weil die Bildung der vorher beschriebenen Wirbelströme bei der Messung durch Verwendung einer „4-terminal-pair“-Messung minimiert wird.
Fazit
Zusammengefasst lässt sich festhalten, dass besonders für die Realisierung von Hochleistungsbatterien die entsprechende Messtechnik benötigt wird. Jeder einzelne Fertigungsschritt spielt dabei eine entscheidende Rolle für das Gesamtergebnis der Batterie.
Für HIOKI ist die enge Zusammenarbeit mit führenden Batterieherstellern über Jahrzehnte ein Garant dafür, sowohl mit etablierter als auch mit neuentwickelter Messtechnik den Batteriemarkt stärken.